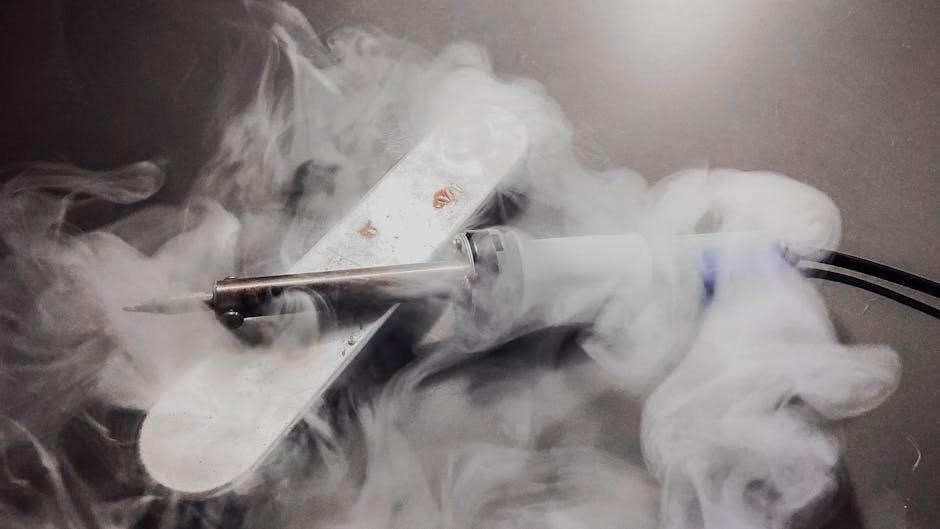
Importance of Maintenance Testing
Maintenance testing is crucial for ensuring equipment reliability, safety, and optimal performance. It identifies potential failures early, reducing downtime and costs. Regular testing also ensures compliance with safety standards and industry regulations, safeguarding both personnel and assets. By verifying system functionality, it helps maintain production efficiency and extends equipment lifespan.
Overview of Industrial Maintenance
Industrial maintenance involves the upkeep of equipment, machinery, and facilities to ensure optimal performance and longevity. It encompasses electrical, mechanical, hydraulic, and pneumatic systems, as well as PLC programming and automation. Maintenance technicians diagnose issues, perform repairs, and implement preventive measures to avoid downtime. Safety protocols are critical, requiring adherence to industry standards. Regular testing and inspections are conducted to identify potential failures early. This field demands a strong understanding of technical principles, problem-solving skills, and the ability to interpret diagrams and manuals. Effective maintenance ensures operational efficiency, reduces costs, and enhances workplace safety.
Importance of Maintenance Testing
Maintenance testing is crucial for ensuring equipment reliability, safety, and optimal performance. It helps identify potential failures early, reducing downtime and operational costs. Regular testing ensures compliance with industry standards and safety regulations, protecting personnel and assets. By verifying system functionality, it supports continuous production and extends equipment lifespan. Effective testing also enhances overall efficiency, reduces unexpected repairs, and ensures systems operate within desired parameters. This proactive approach is essential for maintaining industrial operations smoothly and safely.
Key Topics Covered in Industrial Maintenance Tests
Industrial maintenance tests cover electrical systems, hydraulic and pneumatic mechanisms, PLC programming, and mechanical safety. They also include troubleshooting techniques, preventive maintenance, and interpreting electrical diagrams.
Electrical Systems and Circuits
Electrical systems and circuits are fundamental in industrial maintenance. Tests include understanding voltage measurement using multimeters, circuit analysis, and troubleshooting techniques. Key topics cover series and parallel circuits, circuit breakers, and fuses. Safety protocols like lockout/tagout are emphasized to prevent accidents. Questions often focus on identifying faults in wiring, motor controls, and power distribution systems. Mastery of electrical principles ensures reliable equipment operation and compliance with safety standards. Practical scenarios include diagnosing short circuits and verifying circuit integrity, essential for maintaining industrial productivity and safety.
Hydraulic and Pneumatic Systems
Hydraulic and pneumatic systems are critical in industrial maintenance, relying on fluid and air pressure to operate machinery. Tests cover troubleshooting issues like pump cavitation, fluid leaks, and pressure imbalances. Questions often focus on component identification, such as pumps, motors, and valves. Understanding flow control, pressure regulation, and system efficiency is essential. Practical scenarios include diagnosing pump cavitation and analyzing system performance. Mastery of these systems ensures smooth operation, reduces downtime, and enhances overall industrial productivity and safety, making them a cornerstone of maintenance protocols and procedures.
PLC Programming and Troubleshooting
PLC programming and troubleshooting are essential skills for industrial maintenance technicians. Tests often include questions on ladder logic, programming languages, and troubleshooting techniques. Common issues addressed include faulty I/O cards, communication errors, and incorrect program logic. Practical scenarios involve identifying and resolving errors in PLC-controlled systems. Understanding how to read and modify programs, as well as diagnose hardware and software faults, is critical. Mastery of PLC systems ensures efficient automation, reducing downtime and optimizing industrial processes, making it a vital area of expertise for maintenance professionals.
Mechanical Safety and Preventive Maintenance
Mechanical safety and preventive maintenance are critical for ensuring equipment longevity and workplace safety. Tests often cover procedures for inspecting machinery, identifying wear, and scheduling routine maintenance. Questions may focus on proper lubrication techniques, belt replacements, and aligning motors. Understanding safety protocols, such as lockout/tagout procedures, is essential to prevent accidents. Regular maintenance tasks, like filter changes and bearing inspections, help avoid unexpected failures. Adhering to these practices minimizes downtime, reduces repair costs, and ensures compliance with safety regulations, fostering a safer and more efficient work environment.
Practical Questions and Answers
This section provides real-world scenarios and solutions, covering topics like voltage measurement, hydraulic pump cavitation, and solid-state devices. It helps test-takers apply theoretical knowledge practically.
Common Questions on Voltage Measurement
Voltage measurement is a fundamental skill in industrial maintenance. Common questions include identifying the correct device (multimeter) and understanding safety protocols. Testing for voltage ensures equipment safety and proper functioning. Questions often cover how to interpret readings, distinguish between AC and DC voltage, and recognize potential hazards. Practical scenarios also address troubleshooting voltage drops and verifying circuit live/dead states. These questions reinforce the importance of accurate measurements in maintaining electrical systems efficiently and safely.
Troubleshooting Hydraulic Pump Cavitation
Troubleshooting hydraulic pump cavitation involves identifying causes such as low fluid levels, intake restrictions, or incorrect pressure settings; Common questions address symptoms like noise, vibration, and performance loss. Solutions often include checking the inlet filter, ensuring proper fluid levels, and verifying pressure adjustments. Understanding how cavitation affects pump efficiency and system reliability is critical. Regular maintenance, like cleaning filters and inspecting suction lines, can prevent issues. These questions emphasize practical diagnostic skills for maintaining hydraulic systems effectively and safely.
Understanding Solid-State Devices
Solid-state devices are critical in industrial systems, operating without moving parts, ensuring reliability and efficiency. Questions often focus on identifying devices like thyristors or diodes and their functions. Key terms include “avalanche effect,” associated with specific solid-state components. Understanding these devices is essential for troubleshooting and maintaining electrical systems. Practical questions test knowledge of their applications, such as voltage regulation or signal control. Familiarity with these concepts enhances diagnostic skills, ensuring proper system functionality and safety in industrial environments.
Importance of Practicing with Past Papers
Practicing with past papers enhances exam readiness by familiarizing candidates with question formats, improving problem-solving skills, and boosting confidence through exposure to real test scenarios.
Improving Problem-Solving Skills
Practicing with past papers helps develop strong problem-solving abilities by exposing candidates to diverse industrial scenarios. It enhances analytical thinking, enabling quick identification of faults in electrical circuits, hydraulic systems, and PLC setups. Working through real-world questions improves troubleshooting techniques and adaptability. Candidates learn to approach complex issues methodically, ensuring efficient solutions. Regular practice also sharpens the ability to interpret diagrams and apply theoretical knowledge practically, critical for handling industrial maintenance challenges effectively.
Understanding Exam Patterns
Industrial maintenance tests typically feature multiple-choice questions (MCQs) and true/false formats, assessing knowledge across various topics like electrical systems, hydraulics, and PLCs. The NOTCI test includes 180 questions to be answered in 3 hours, reflecting the exam’s rigorous structure. Familiarizing oneself with this pattern aids in strategic preparation, enhancing time management and reducing exam-day anxiety. Understanding the distribution of topics and question types allows candidates to focus their study efforts effectively, ensuring comprehensive readiness for the actual test.
Boosting Confidence for the Actual Test
Practicing with past papers and mock tests is essential for building confidence. Regularly solving industrial maintenance questions helps familiarize candidates with the exam format and content. Focusing on weak areas identified through practice strengthens overall readiness. Additionally, reviewing answers and explanations enhances understanding and reduces exam-day anxiety. Using resources like PDF guides and online platforms provides structured preparation, ensuring candidates feel prepared and self-assured. Consistent practice with realistic test simulations boosts familiarity and confidence, leading to better performance in the actual test.
Resources for Preparation
Utilize recommended PDF guides, online platforms, and flashcards for key terms. These resources provide comprehensive practice questions, detailed explanations, and structured study materials to aid preparation effectively.
Recommended PDF Guides
Download comprehensive PDF guides like the “Industrial Maintenance Technician Test” with 83 practice questions and answers. These guides cover essential topics such as electrical systems, hydraulics, pneumatics, and PLC programming. They provide detailed explanations for each question, helping you understand key concepts. Available on platforms like Docsity, these resources are ideal for self-study and exam preparation. Flashcards and multiple-choice questions are also included to reinforce learning. These PDFs are a valuable tool for mastering industrial maintenance concepts and acing the test.
Online Platforms for Practice Tests
Enhance your preparation with online platforms offering industrial maintenance practice tests. Websites like Quizlet provide interactive tools, flashcards, and multiple-choice questions to assess your knowledge. These platforms simulate actual exam formats, covering topics such as troubleshooting, safety protocols, and preventive maintenance. They offer real-time feedback and detailed explanations to help you improve. Additionally, platforms like Docsity host comprehensive practice exams with questions on electrical systems, hydraulics, and PLC programming. Utilize these resources to refine your skills and gain confidence for the actual test.
Flashcards for Key Terms
Flashcards are an excellent tool for memorizing essential terms and concepts in industrial maintenance. Platforms like Quizlet offer digital flashcards covering topics such as electrical systems, mechanical components, and PLC programming. Key terms include voltage, amperes, and solid-state devices, with definitions and practical examples. Flashcards also focus on safety protocols, hydraulic systems, and troubleshooting techniques. They provide a quick and effective way to review critical concepts, helping you master the terminology and principles required for success in industrial maintenance tests and real-world applications.
Exam Format and Structure
The industrial maintenance test includes 180 questions to be completed in 3 hours, featuring multiple-choice and true/false formats. Questions cover electrical systems, hydraulics, PLCs, and safety protocols, ensuring comprehensive assessment of technical knowledge and practical skills.
Number of Questions and Time Limit
The industrial maintenance test typically consists of 180 questions, which candidates must complete within a 3-hour time frame. This format ensures a thorough assessment of knowledge and problem-solving skills. The time limit is designed to simulate real-world scenarios, where technicians must diagnose and resolve issues efficiently. The large number of questions covers a wide range of topics, from electrical systems to safety protocols, ensuring comprehensive evaluation of a candidate’s expertise in industrial maintenance. Proper time management is essential for success in this exam.
Types of Questions (MCQs, True/False)
Industrial maintenance tests feature multiple-choice questions (MCQs) and true/false formats to assess a wide range of knowledge. MCQs evaluate understanding of complex topics like PLC programming and hydraulic systems, while true/false questions test familiarity with safety protocols and basic principles. Some exams also include short-answer and scenario-based problems to gauge practical problem-solving skills. This variety ensures a comprehensive evaluation of both theoretical knowledge and hands-on expertise, preparing candidates for real-world challenges in maintenance roles.
Weightage of Each Topic
Industrial maintenance tests allocate varying weights to topics based on importance. Electrical systems and circuits often have the highest weightage, followed by hydraulic and pneumatic systems. PLC programming and troubleshooting typically account for a significant portion, while mechanical safety and preventive maintenance are also emphasized. Advanced topics like interpreting electrical diagrams and building codes may have moderate weightage. Understanding the distribution helps candidates focus their study efforts effectively, ensuring they prioritize high-weight areas for better exam performance.
Tips for Effective Test Preparation
Focus on understanding key concepts, practice with past papers, and use flashcards for memorization. Allocate time for each topic based on its weightage in the exam.
Creating a Study Schedule
A well-structured study schedule is essential for effective preparation. Allocate specific time slots for each topic, focusing on key areas like electrical circuits, hydraulics, and PLC programming. Dedicate 30% of your time to theoretical concepts and 70% to practical problems. Incorporate regular practice tests to assess progress and identify weak areas. Review past papers to familiarize yourself with exam patterns. Set achievable daily goals and stick to them consistently. Use flashcards for quick revision of key terms and formulas. Ensure regular breaks to maintain focus and avoid burnout. Adjust the schedule as needed based on performance.
Focus Areas for Maximum Scoring
Identify key areas that are frequently tested, such as electrical circuits, hydraulics, and PLC programming. Focus on understanding fundamental principles like voltage measurement and hydraulic pump troubleshooting. Prioritize topics with higher weightage, such as mechanical safety and preventive maintenance. Strengthen problem-solving skills by practicing numerical problems and scenario-based questions. Review past papers to understand exam patterns and refine time management. Emphasize practical applications over theoretical knowledge to maximize scoring potential in industrial maintenance tests.
Strategies for Time Management
Evaluate questions quickly and prioritize those you can answer confidently. Allocate time based on question difficulty and weightage. Use practice tests to simulate exam conditions and refine your pacing. Skim through the entire paper first to identify straightforward questions. Avoid spending too long on a single question—move on and return if time permits. Manage breaks wisely during long study sessions to maintain focus. Develop a mental timer to track progress, ensuring efficient use of the allotted time for optimal performance in industrial maintenance tests;
Common Mistakes to Avoid
Overlooking safety protocols, neglecting basic electrical principles, and not practicing enough PLC problems are common pitfalls. Ensure attention to detail and thorough preparation to avoid these errors.
Overlooking Safety Protocols
Overlooking safety protocols is a critical mistake in industrial maintenance. Neglecting proper procedures can lead to accidents, injuries, and equipment damage. Always prioritize personal protective equipment, lockout/tagout processes, and adherence to industry standards. Skipping safety checks can result in failed inspections and legal consequences. Understanding safety protocols is essential for both workplace safety and exam success, as they are frequently tested in industrial maintenance exams. Familiarize yourself with emergency procedures and equipment safety guidelines to avoid such errors and ensure a safe working environment.
Neglecting Basic Electrical Principles
Neglecting basic electrical principles is a common mistake in industrial maintenance. Ignoring fundamental concepts like voltage, current, and resistance can lead to incorrect diagnoses and unsafe repairs. Forgetting to use proper measurement tools, such as multimeters, can result in inaccurate assessments of electrical systems. Overlooking circuit load capacities and wiring standards can cause equipment damage or safety hazards. Understanding Ohm’s Law and circuit analysis is essential for troubleshooting. Such oversights can lead to failed inspections and pose significant risks to both personnel and equipment operation. Always review electrical fundamentals before performing maintenance tasks.
Not Practicing Enough PLC Problems
Not practicing enough PLC problems is a common oversight in industrial maintenance preparation. PLCs are core to modern automation, and insufficient practice can lead to difficulty in troubleshooting and programming. Many technicians struggle with I/O card diagnostics and ladder logic interpretation due to lack of hands-on experience. Without regular practice, even basic tasks like identifying faulty inputs or correcting program errors become challenging. This can result in prolonged downtime and safety risks. Regularly solving PLC-related questions and scenarios is essential for building proficiency and ensuring reliable system operation.
Role of Safety in Industrial Maintenance
Safety is critical in industrial maintenance to prevent accidents, protect equipment, and ensure compliance with regulations. It involves protocols, proper training, and emergency preparedness to safeguard personnel and assets.
Industrial and Mechanical Safety Basics
Industrial and mechanical safety basics are essential to prevent accidents and ensure smooth operations. They involve adhering to safety protocols, proper training, and regular equipment inspections. Key components include personal protective equipment (PPE), lockout/tagout procedures, and hazard identification. Understanding electrical safety, such as voltage measurement using multimeters, is critical. Mechanical safety includes proper tool usage and machinery guarding. Regular risk assessments and emergency preparedness further enhance safety. Compliance with industry standards and regulations is mandatory. Following these basics minimizes risks, protects personnel, and maintains operational integrity.
Importance of Safety Protocols
Safety protocols are vital in industrial maintenance to prevent accidents and protect personnel. They ensure compliance with industry regulations and standards, minimizing risks. Proper safety measures, such as lockout/tagout procedures and PPE usage, safeguard workers. Regular equipment inspections and hazard assessments reduce potential dangers. Adherence to safety protocols also enhances operational efficiency and maintains a responsible work environment. By prioritizing safety, industries can avoid costly downtime and legal issues, ensuring long-term sustainability and employee well-being. Safety protocols are the cornerstone of effective industrial maintenance practices.
Case Studies on Safety Violations
Case studies highlight the consequences of neglecting safety protocols in industrial maintenance. For instance, bypassing lockout/tagout procedures led to equipment startup during maintenance, causing severe injuries. Another incident involved improper use of personal protective equipment (PPE), resulting in chemical exposure. These examples underscore how safety violations can lead to accidents, downtime, and legal repercussions. Analyzing such cases helps identify root causes and improves safety practices. Learning from these incidents ensures safer working conditions and prevents future violations, fostering a culture of compliance and responsibility.
Advanced Topics in Industrial Maintenance
Advanced topics include interpreting electrical diagrams, understanding building codes, and mastering troubleshooting techniques. These skills are essential for diagnosing complex issues and ensuring compliance with industry standards.
Interpreting Electrical Diagrams
Interpreting electrical diagrams is a critical skill for industrial maintenance technicians. These diagrams provide detailed visual representations of electrical systems, including circuits, components, and connections. Technicians must identify symbols, understand wiring layouts, and trace circuits to diagnose issues. Proficiency in reading diagrams ensures accurate troubleshooting and repair. Common elements include power sources, switches, motors, and control devices. Using tools like multimeters, technicians verify voltage and current readings against diagram specifications. This skill is essential for maintaining safety, efficiency, and compliance with industry standards in industrial settings.
Understanding Building Codes
Building codes are essential for ensuring safety and compliance in industrial settings. They outline standards for electrical, plumbing, and mechanical systems, guaranteeing installations meet safety requirements. Codes like the National Electric Code (NEC) regulate wiring and equipment installation, while others cover fire safety and structural integrity. Compliance with these codes is legally required and critical for protecting personnel and assets. Understanding building codes helps technicians identify potential hazards and ensure systems operate within legal and safety guidelines, reducing risks and liabilities in industrial environments.
Advanced Troubleshooting Techniques
Advanced troubleshooting involves systematic approaches to diagnose complex issues in industrial systems. Techniques include root cause analysis, predictive maintenance, and the use of diagnostic tools like multimeters and thermal imaging cameras. Understanding electrical circuits, hydraulic systems, and PLC programming is critical for identifying faults quickly; Emerging technologies, such as AI-driven diagnostic software, further enhance problem-solving efficiency. These methods enable technicians to resolve issues effectively, minimizing downtime and ensuring optimal system performance. Mastery of these techniques is vital for industrial maintenance professionals to handle modern, intricate equipment and systems successfully.
Mastering industrial maintenance tests requires thorough preparation, practice, and staying updated with industry trends. Utilize resources like PDF guides and online platforms to enhance your skills and confidence for success.
Final Tips for Success
To excel in industrial maintenance tests, create a structured study schedule and identify focus areas for improvement. Practice with past papers and simulated exams to familiarize yourself with the format. Understand exam patterns and time management strategies to optimize your performance. Regularly review safety protocols and basic electrical principles to avoid common mistakes. Stay updated with industry trends and advancements in maintenance technologies. Consistent practice and thorough preparation are key to achieving success and boosting confidence for the actual test.
Staying Updated with Industry Trends
Staying updated with industry trends is essential for success in industrial maintenance. Advances in technology, such as smart sensors and IoT, are reshaping maintenance practices. Engage with online platforms, webinars, and publications to stay informed. Participate in forums and communities to share insights and learn from peers. Regularly reviewing updated standards and codes ensures compliance. Leveraging these resources enhances your knowledge and prepares you for evolving challenges in the field. This proactive approach not only boosts exam readiness but also advances your career in industrial maintenance.